Material selection plays a big role in sheet metal fabrication. Budget and lead times matter, but so do corrosion resistance, environmental conditions, and coating compatibility. Ignoring these factors can lead to faster wear, higher finishing costs, or even product failure.
Edge Fabrication works with a variety of metals for industrial use. Picking the right one early on can improve durability, appearance, and cost-efficiency. Here’s a quick breakdown of the most common materials we use and when to consider each.
STAINLESS STEEL (304, 316/316L, 430)
304 stainless steel is a reliable option for general outdoor applications. For environments exposed to salt, moisture, or chemicals, 316/316L offers enhanced corrosion resistance and it can be used in industries such as water treatment and mining. When cost is a primary concern, 430 stainless provides a more economical alternative while still offering basic protection in less demanding conditions.
ALUMINUM (5052, 6061)
5052 is a widely used aluminum grade in sheet metal fabrication, known for its excellent corrosion resistance and strong performance in marine or high-humidity environments. Its flexibility and formability make it well suited for parts that require shaping or bending.
6061 aluminum provides a dependable combination of strength, corrosion resistance, weldability, and machinability. Though not the strongest aluminum available, it offers a solid balance of properties that make it a popular choice for structural components and enclosures where durability is important. 6061 is not a typical material for bending as it can easily fracture.
RAW STEEL (CRS, HRPO)
Cold Rolled Steel (CRS) and Hot Rolled Pickled and Oiled (HRPO) are both commonly used in general-purpose sheet metal fabrication. These materials offer excellent formability with minimal concerns during bending, welding or post-production operations. However, they do not include inherent corrosion resistance and should be powder coated, plated or galvanized when used in environments with moisture or exposure.
CRS features a smooth finish and is generally easier to work with. HRPO, often used in thicker applications above 0.125″, has a black scale surface that makes it less forgiving during fabrication. For both materials, hot dip galvanizing is an option, though material
thickness under 0.250″ to 3/8″ can lead to potential distortion. Raw cut edges remain unprotected and should be addressed during design.
PRE-COATED STEEL (Galvanized, Galvannealed, Pre-Painted)
Pre-coated steel offers built-in corrosion protection and is frequently selected for outdoor enclosures, HVAC equipment, and other exposed-use applications.
Galvanized steel (G90/G60) and Galvannealed steel (A60) both provide medium corrosion resistance. Galvanized material may present off-gassing issues when powder coated, while Galvannealed options are better suited for paint adhesion and can be coated for additional protection.
Pre-Painted Steel comes with a factory-applied finish, making it ideal for applications with specific color or aesthetic requirements. However, this finish can crack or deform depending on the design and forming requirements. It’s important to evaluate these factors early in the project to ensure the material aligns with the intended form and function. As with other pre-coated materials, raw cut edges typically have limited corrosion resistance and may need additional treatment depending on the end use.
Material selection is more than a box to check, it influences durability, corrosion resistance, fabrication time, and finishing needs. Whether the application calls for stainless steel, aluminum, raw steel, or pre-coated options, choosing the right material from the start can help reduce rework, extend product life, and meet performance standards with confidence.
For production-grade precision sheet metal parts, matching the material to the job is key to achieving both reliability and efficiency. To discuss material options or request a quote, visit the Contact Us page and connect with the Edge Fabrication team.
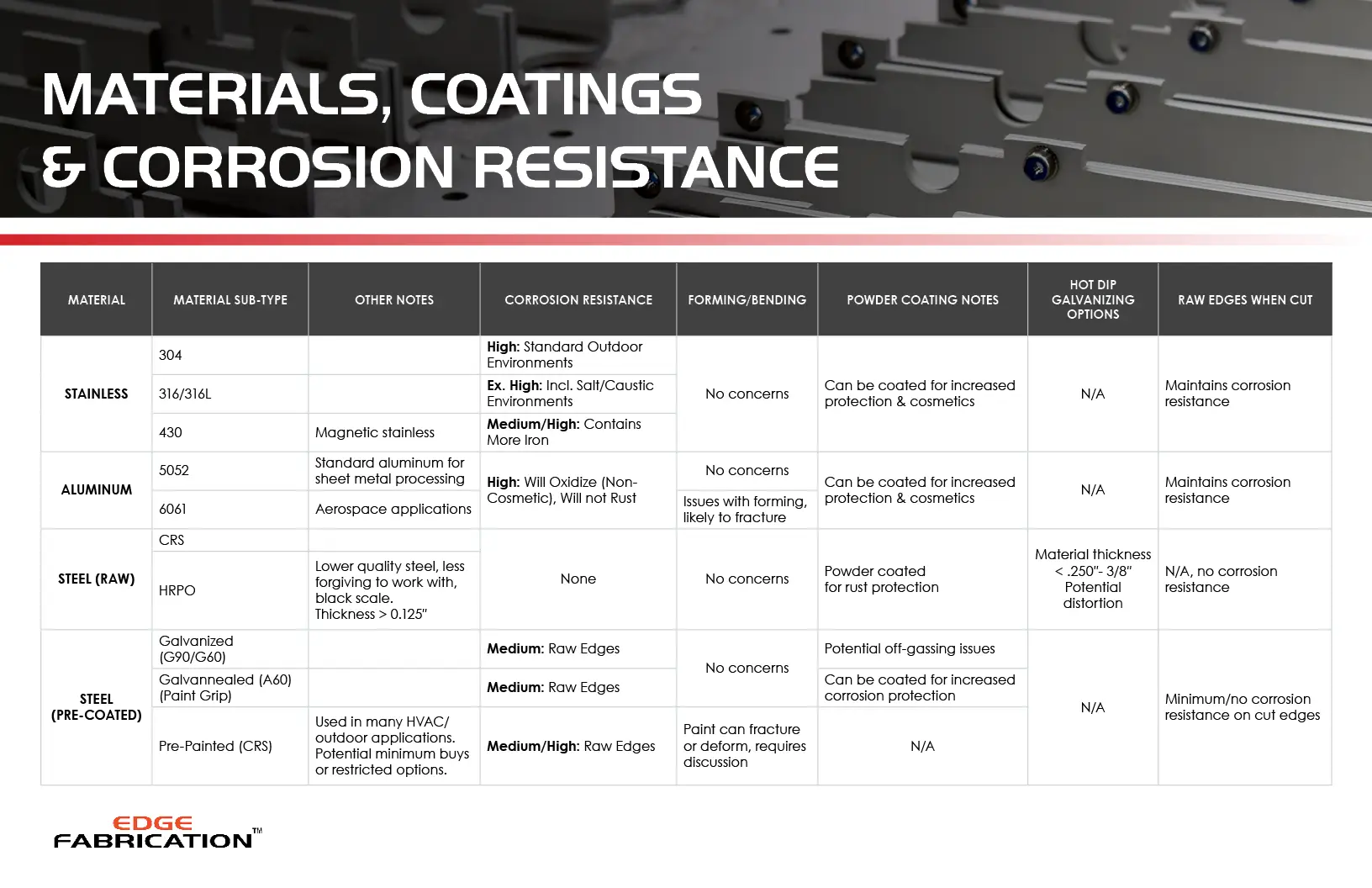